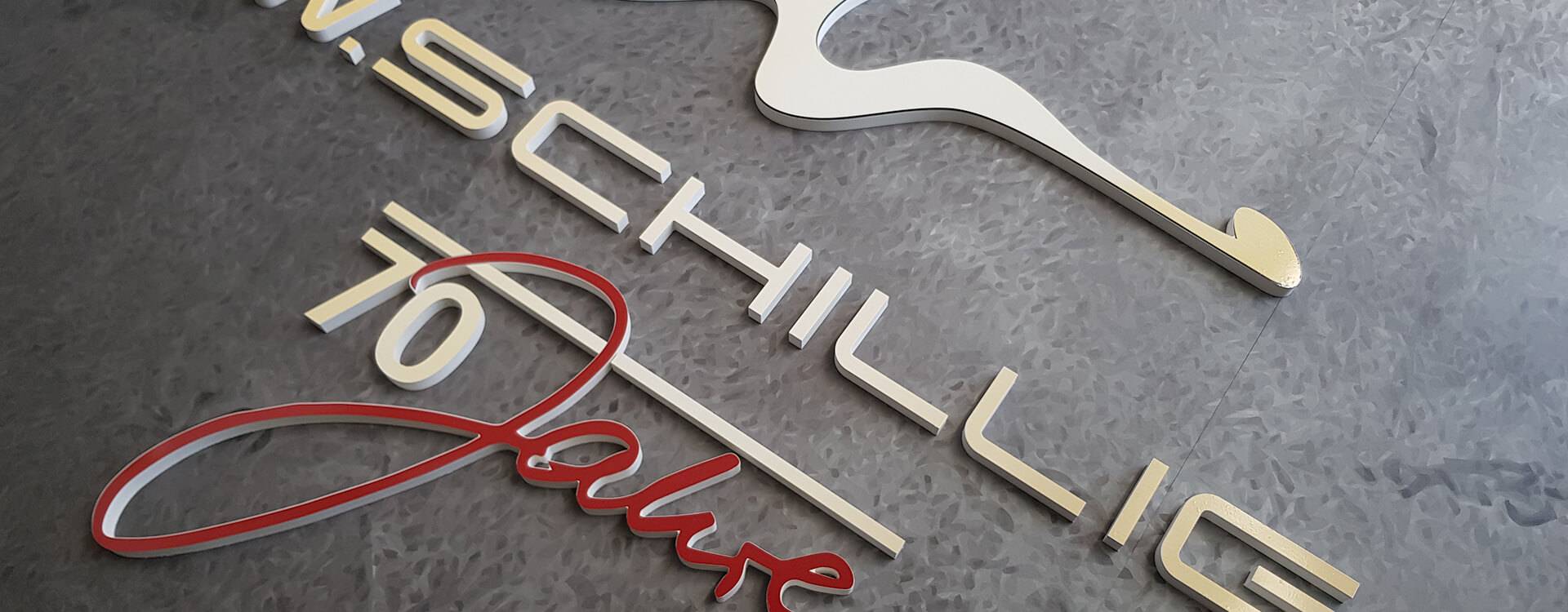
How furniture is created
The prototype: from the idea to the finished sofa
New furniture is not developed from the vacuum. The spirit of the times plays a role – in times of global change, people want more security and warmth, evident in especially soft, cuddly furniture and warm, earthy colours.
Ergonomics play an important role
Ultimately, ergonomics play an ever increasingly important role: Good furniture must not only be beautiful, but foremost be comfortable and provide best possible support for increased numbers of users with back impairments. The designer must feel, absorb and incorporate all these factors. At the same time, the new furniture must look good, be unproblematic in manufacturing and, most of all, be affordable. So the task presented to the designer and the team of upholsterers, seamstresses and constructing engineers in the development department is not an easy one. Last, but not least, is one thing important: year-long experience and an instinctive »gut-feeling«, letting one sense if an idea can lead to success.
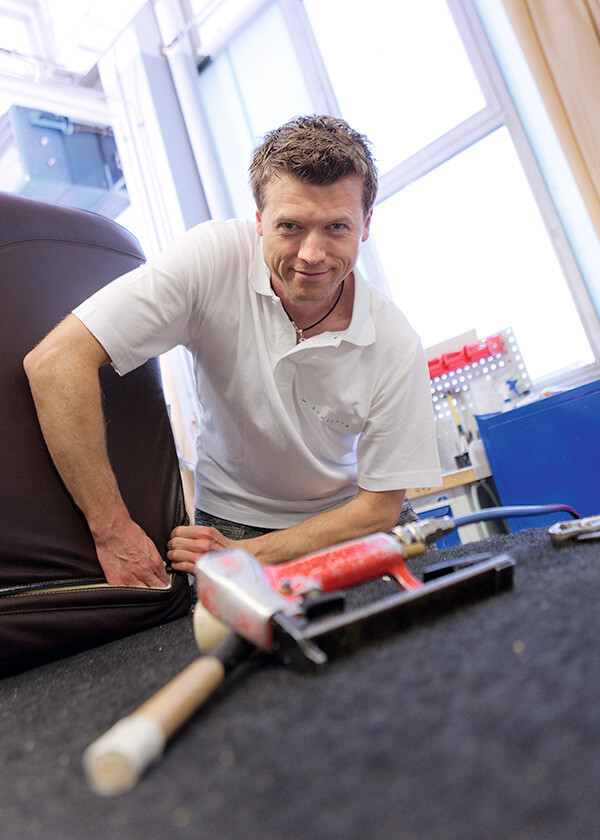
Tracking the sofa For all who want to know it exactly, we give you exciting insights behind the scenes
1. Cutting
Here the experience of our employees is in great demand! Up to seven hides are needed for a normal-sized leather sofa. These are checked by the cutters for unsightly flaws such as scars, brand marks etc. Then, every individual piece of the sofa is marked on the hide and the corresponding pieces cut by hand according to template. After a final inspection, the cut pieces are sent to the sewing department. Single-coloured fabrics or fabrics with very small patterns, however, can be prepared on the fabric cutter. A vacuum sucks the fabric down onto the cutting table. The single pieces are then automatically cut according to a pre-made template.
2. Fleece
When cutting fleece, many layers of fleece are placed on top of each other on a long table, covered with plastic foil and a vacuum is applied, pressing all layers together. This way, several layers of fleece can be marked and cut at the same time. The furniture becomes soft and cuddly by using fleece.
3. Leather edging
Thick leather must be bevelled in the areas where the seams will be, otherwise it will not be possible to sew the seams with a sewing machine.
4. Sewing department
The first step is to sew together the fleece and the leather/fabric pieces that are to be particularly soft (e.g. outer edging, seat and back cushions etc.). Hereafter, single pieces are gathered on a special machine. This is the terminology for »deliberately adding folds« to create a casual look to the furniture. Only then are the still separate pieces placed on the sewing assembly line. Our qualified specialists sew together approx. 220 parts per suite to create a cover for the furniture. One employee sews the complete suite so as to maintain a uniform look. Later on, the contrast stitch is applied with the double-needle sewing machine. Every cover is carefully checked for flaws in a final inspection.
5. Filling cushions
Strength is needed here! The upholstery covers coming from the sewing department are filled by hand with large seat and back cushions. For safety measures and for better durability, the cushions are glued on the bottom.
6. Pre-upholstery
Massive beech hardwood is the ideal material for especially durable and long-lasting furniture frames and thus is used for the frame and supporting connecting parts. The bonding and the dowelling as well as assembling the pieces are done by hand. The seat is equipped with nosag-springs. The fastenings for the nosag-springs are sturdily attached by hand to the frame with pre-determined spacing. Strong elastic-webbing is used in the back. Finally, the frame is encased with foam and fleece.
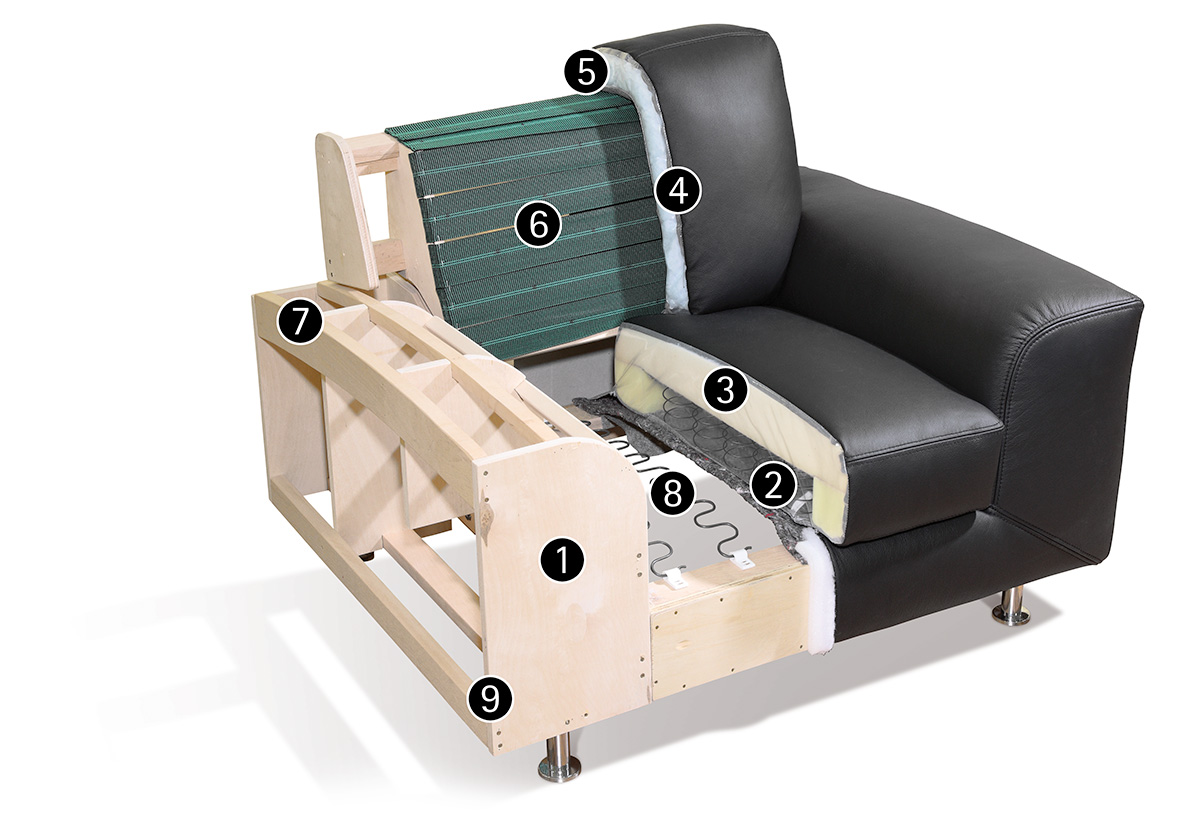
Furniture quality: a look inside
- Beech frame The frame and supporting connecting parts are made of beech hardwood in optimized cross-sections. Beech is a renewable resource.
- Spring core Most models are available with a spring core. W.SCHILLIG uses spring cores from reputable German manufacturers!
- Cushioning High-density cushion foam (in the seat starting from 35 kg/m³) guarantees perfect seating comfort even after years of intensive use!
- Sawafill fleece This high-quality synthetic fleece provides for cosy, soft seating comfort and a modern, casual look (is attachedto or gluedon the quilted back cushion).
- Chamber cushions are used in many models. They adapt to the back perfectly and keep their shape permanently due to premium filling materials.
- Elastic webbing in the backrest acts as an additional suspension for soft, long-lasting flexible support of the body.
- Plywood side frame All cuts for stress areas (e.g. side parts) are made of plywood and offer the same stability as massive hardwood.
- Nosag-suspension Incorporating nosag-suspension is the best way to provide permanent, ergonomic support.
- Hand-crafted connections side pieces and frame are dowelled, massive woods base-stabilized: manufacturing with traditional handicraft in time-tested durability.
7. Upholstery department
The upholstery department is the heart of the production (comparable to the final assembly for automobiles)! Only the highest quality materials are used according to strict DGM regulations, and the experience of the employees is of utmost importance! The filled cushions from point 5) are draped onto the upholstered frame from point 6) and optional functional hinges attached. The cover is tightened and nailed onto the frame. Finally, the draped back cover is aligned. With the help of spanning strips, the cover can then be fastened to the frame. It is especially important to neatly upholster the edges, the front side and the facing. Plastic feet are attached for safe and careful delivery.
8. Quality control
Every piece of furniture undergoes thorough inspection. At the final quality control, the craftsmanship, seating comfort and all existing functions are checked. The flawless quality is then documented with digital photographs, to rule out later complaints. Only after successfully passing all tests may the furniture be packed and shipped. For each order, product information is also gathered for delivery.
9. Delivery
An affiliated logistics company provides for safe and careful transport to the customer.
Handicraft at its best
A perfectly organised workflow is the basis for quality, good service and on-time delivery. The production flow is fully computerized, providing smooth processing. Barcodes inform about each production stage of every piece of furniture. The assembly of high-quality mechanical functions is done in a special assembly line. Constant quality control is standard. Before the furniture is dispatched, it is packed in recyclable special foil to prevent pressure marks. Reliable transport is provided by the trained staff and an affiliated logistics company.
Furniture built with precision
One can seriously fall in love with the design of a furniture piece. Excellent manufacturing is mandatory. Leather is a challenging and valuable material, where every detail must be fabricated with great care. No leather is alike, that’s why perfect raw material and precise material testing is especially important.
W.SCHILLIG – a leather specialist
As a leather specialist, we also know that the manufacturing of leather requires special skills, a high degree of responsibility, and a love for the trade. Here, we rely on our trained workers.
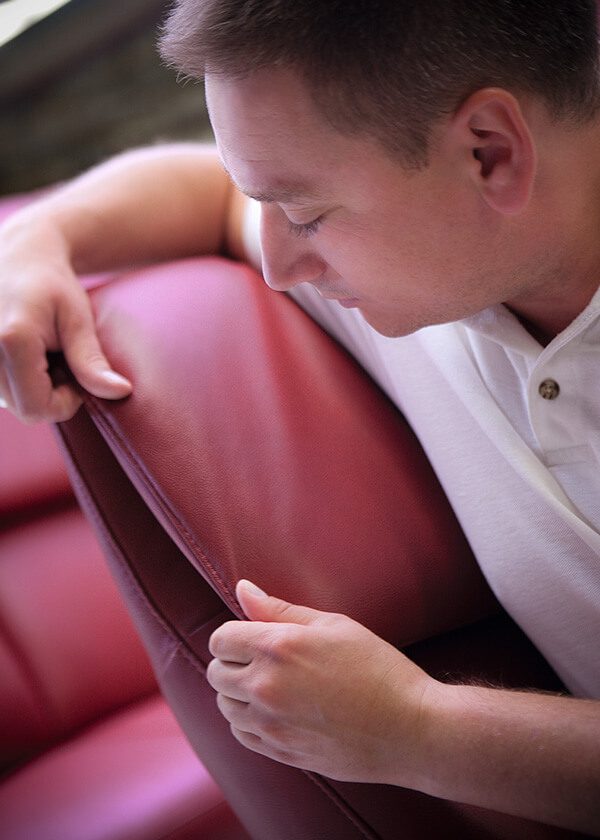